back
Best Practices for Maintaining and Repairing Industrial Equipment in Your Property
04-2023
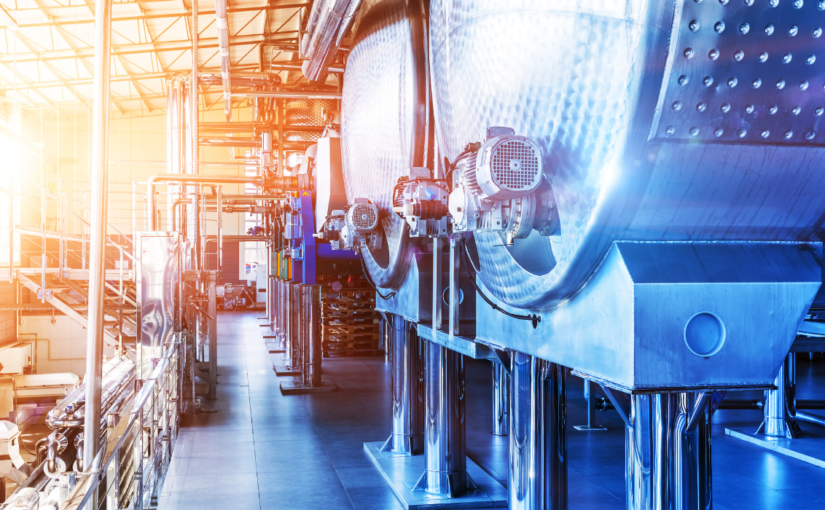
Any property, whether it be a factory, warehouse, or manufacturing plant, needs industrial equipment to function. Equipment can malfunction or break down without the required maintenance and repairs, resulting in expensive downtime and sometimes dangerous circumstances for workers. Developing best practices for maintaining and repairing industrial equipment is crucial to preventing these problems. We’ll go over some of the most significant best practices for maintaining and repairing industrial equipment in this blog post.
- Create a Maintenance Schedule: Setting up a maintenance program is the first step in maintaining industrial equipment. The frequency and kind of maintenance needed for each piece of equipment should be specified in this schedule. For instance, some equipment can need daily maintenance, while other equipment might just need monthly servicing. You can make sure that all equipment is routinely serviced and that problems are found before they become serious ones by developing a maintenance program.
- Conduct Regular Inspections: It’s critical to perform routine inspections of industrial equipment in addition to scheduled maintenance. Inspections can aid in the early detection of problems, enabling timely repairs and averting the emergence of more serious difficulties. Equipment should be examined for wear and tear, leaks, and other potential issues during inspections. Any problems found should be fixed right away.
- Train Employees on Proper Use and Maintenance: Industrial equipment’s longevity and performance depend on proper use and maintenance. It is crucial to offer training to guarantee that workers are operating machinery correctly and carrying out maintenance duties properly. Topics including safety protocols, appropriate usage, and maintenance duties should be covered in this training. You can reduce the likelihood of accidents and equipment failure by training your personnel.
- Keep Records: Tracking equipment performance and spotting trends requires keeping records of maintenance and repairs. Additionally, these records can be utilized to show adherence to safety guidelines and to back up maintenance claims in the event of an accident. The date of maintenance or repair, the equipment that was serviced, the work that was done, and any parts or materials that were utilized should all be included in the records.
- Follow Manufacturer Recommendations: Industrial equipment manufacturers frequently offer maintenance and repair advice. To make sure that equipment operates as intended and keeps up its good condition, these suggestions should be strictly followed. Equipment failure, voiding of warranties, and safety issues can all come from disregarding manufacturer advice.
- Address Issues Promptly: Industrial equipment problems should be fixed very once whenever they are discovered. Delaying repairs can result in more serious issues and more expensive remedies. Additionally, personnel may be in danger from equipment that is malfunctioning. It is important to identify and rectify problems as soon as they are discovered.
- Use High-Quality Replacement Parts: Whenever industrial equipment needs replacement parts, it’s crucial to choose high-quality components. Equipment failure and safety issues might come from the use of subpar or incompatible parts. To ensure compatibility with the equipment being repaired, replacement parts must be obtained from reliable vendors.
- Implement a Preventative Maintenance Program: Regular maintenance procedures are part of preventative maintenance plans, which are intended to stop equipment breakdown and save downtime. Tasks like cleaning, lubrication, and component replacement can be part of this list. Establishing a preventative maintenance program will help you extend the lifespan of your industrial machinery and lower the likelihood of expensive downtime.
- Conduct Regular Testing: Industrial machinery needs to be tested frequently to make sure it is operating properly and to find any potential problems. Performance testing, stress testing, and load testing are examples of tasks that might be included in testing. You may find problems before they become serious ones and make sure that equipment is operating properly by regularly testing it.
- Work with a Trusted Maintenance and Repair Provider: Working with a reputable industrial equipment maintenance and repair company is crucial. This service provider should be able to offer quick and dependable service and should have experience working with the particular type of equipment you need. Another crucial aspect of maintenance and repair is regular communication, which enables early problem detection and rapid resolution. You can ensure that your industrial equipment is properly maintained and serviced, reducing downtime and maximizing performance, by partnering with a dependable provider.
In conclusion, industrial equipment maintenance and repair are crucial to the efficient operation of any property. You can make sure that your industrial equipment works as intended and stays in good condition by putting best practices into practice, such as creating a maintenance schedule, performing routine inspections, training employees, keeping records, adhering to manufacturer recommendations, addressing issues as soon as they arise, using high-quality replacement parts, implementing a preventative maintenance program, performing routine testing, and working with a dependable maintenance and repair provider. You can limit equipment downtime, lower repair costs, and guarantee employee safety by giving equipment maintenance and repair first priority.
F2H Capital Group is a debt advisory firm specializing in negotiating the best terms for your commercial real estate projects. The company offers a range of financial products and services, including fixed loans, bridge loans, and construction loans across all asset types. Please contact us for any of your financing needs.